Le Lean Management : l’amélioration continue dans l’esprit « Kaizen »
Le Lean Management, que l’on désigne plus rarement sous les appellations de « gestion sans gaspillage », « gestion allégée », « gestion au plus juste » ou tout simplement « Lean », est une méthode de gestion de la production basée sur l’amélioration continue à travers des changements mineurs et progressifs pour améliorer la performance au sens large.
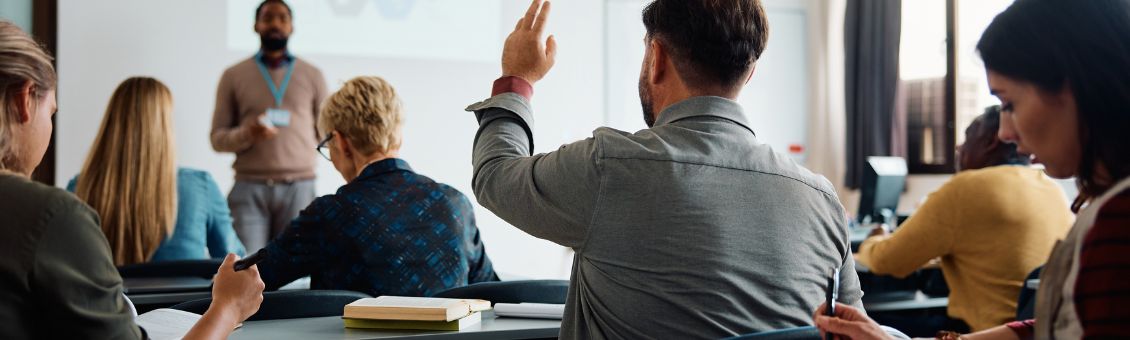
Le contexte de naissance du Lean Management
Pendant les Trente Glorieuses, le défi des entreprises résidait dans la capacité de production, la demande étant virtuellement « infinie ». Les biens et services proposés étaient majoritairement standards, sans possibilité de personnalisation. C’est d’ailleurs ce contexte de production indifférenciée qui a fait émerger le Taylorisme ainsi que l’Organisation Scientifique du Travail (OST), deux concepts qui visaient à faire en sorte que les travailleurs soient interchangeables, dopant la demande en main d’œuvre peu (ou pas) qualifiée. L’improvisation, l’innovation et l’expérimentation n’avaient donc pas leur place dans l’entreprise.
Le macroenvironnement dans lequel les entreprises évoluaient changera progressivement à partir du milieu des années 1975. La demande baissait progressivement en quantité tout en exigeant des produits plus sophistiqués. Les limites de l’OST ont donc commencé à se faire sentir.
Inventé dans les usines de production de Toyota par Taiichi Ohno dans les années 1950, le Lean a suscité un bel engouement en Amérique du Nord et en Europe, en réponse aux problématiques de la surproduction, du gaspillage des matières premières, des lenteurs dans la production, des processus de transport inefficients ou encore des charges cachées liées aux contretemps de la bureaucratie d’entreprise. Le Lean est donc venu épingler les « usines à gaz » pour épurer les processus et recentrer les actions sur l’essentiel. Il s’agit donc d’une stratégie d’excellence opérationnelle qui vise à traquer et à éliminer le gaspillage des ressources, qu’elles soient matérielles ou immatérielles. Pour travailler sa flexibilité face aux turbulences du marché et améliorer sa compétitivité, l’entreprise devait donc s’émanciper du modèle dual de l’expert qui décide et de l’opérateur qui exécute. En effet, qui de mieux que le salarié pour proposer des idées d’amélioration de son poste de travail ?
Le Lean Manager, garant de l’esprit « Kaizen »
Le Lean Management appelle une certaine polyvalence des profils pour favoriser la mutualisation des ressources et l’interaction entre les différents collaborateurs pour maximiser la valeur ajoutée réalisée par l’entreprise. Projets transverses, équipes pluridisciplinaires et processus formalisés d’amélioration continue permettent à l’entreprise de travailler « mieux » plutôt que de travailler « plus vite ».
Dans cette organisation, le management s’affranchit de son rôle de « juge » qui distribue les bons points et les sanctions pour se positionner en garant de l’esprit « Kaizen », une philosophie japonaise qui sous-tend le Lean Management. Pour résumer, l’esprit Kaizen défend l’idée selon laquelle « l’amélioration est infinie », qu’elle commence « chez soi » et « maintenant ». Le Lean Management sort donc l’entreprise de son organisation en silos pour lui permettre de prendre de la hauteur et déployer une vue panoramique sur la chaîne de valeur afin de rationaliser la prise de décision et doper sa rentabilité. Le Lean Management s’attaque :
- au Muda : les actions qui n’ajoutent rien au produit final ou, du moins, rien qui ne soit perçu comme « utile » par le client ;
- au Muri : la surcharge de travail induite par les processus non adaptés et non optimisés comme un ERP compliqué, un parc informatique obsolète ou encore des bureaux/ateliers trop éloignés les uns des autres ;
- au Mura : l’irrégularité, tout ce qui ne permet pas de planifier, comme un fournisseur à la capacité d’approvisionnement variable ou encore une machine au rendement irrégulier.
Lean Management : la preuve par l’exemple
Tokheim est une entreprise spécialisée dans la conception et la fabrication de pompes à essence dans le Calvados. Dans le cadre d’une grande remise en question de sa méthode de travail minée par l’urgence et les approximations, Tokheim s’est inspirée des principes du Lean Management pour élaborer sa stratégie « Takt Time ». Au programme :
- réévaluation de l’importance de la demande sur le marché ;
- répartition de la création de la valeur sur trois filiales spécialisées ;
- mise en place d’une feuille de route pour chaque produit ;
- création de marquages au sol pour identifier d’un simple coup d’œil l’étape par laquelle passe chaque pompe dans la ligne de production ;
- délocalisation des ateliers de réparation pour préserver la fluidité du travail ;
- installation de roulettes sur les pompes pour faciliter le déplacement des produits finis et semi-finis, etc.
Résultat : réduction des délais de production, baisse du coût de stockage de 60 % et amélioration du taux de respect des délais qui caracole désormais à 98 %. De son côté, la célèbre marque de machines agricoles John Deere a pu réduire son coût de revient et ses délais de production en automatisant toute la partie du contrôle qualité et en identifiant les fragments « inutiles » ou « non significatifs » du processus de production.
Il y a autant de matérialisations du Lean Management qu’il y a d’entreprises. Il appartient aux équipes de réaliser un véritable travail de recensement, d’analyse et d’expérimentation pour « fabriquer » une méthodologie Lean en phase avec le secteur d’activité, la taille et la culture de l’entreprise.
Passionné par le management et la conduite du changement ? Le Groupe IGENSIA Education (ex Groupe IGS), à travers l'École de finance d’entreprise et de Management, prépare les futurs cadres d’entreprise et les entrepreneurs à développer leur volume d’affaires, à recruter, à manager et à optimiser leurs ressources.